CASE STUDY活用事例
自動車業界での活用
- 品質向上
- 開発期間短縮
- Studio システム
自動車業界では生産速度向上、複雑形状のパーツ製造、コスト削減、軽量化など多様な課題に日々取り組んでいます。Desktop Metalの金属3Dプリンターはこうした課題を解決し、自動車開発に貢献します。
01 導入
1世紀以上前、ヘンリーフォードはTモデルの工場に最初のシンプルな移動組立ラインを導入し、そこから自動車製造は永遠に変化しました。
組み立てラインが当時の業界で新しい扉を開いたのと同じように、積層造形の台頭は自動車製造のライフサイクルの全ての段階、機能的なプロトタイピングから中量および大量生産、アフターマーケットおよびスペアパーツへの生産において新しい機会を生み出します。
そして、それらの機会の多くは、生産速度とパーツの複雑さ、またはその2つの組み合わせと関係します。
従来と同じ制限に縛られていないため、3Dプリンティングはデザイナーやエンジニアが広大な新しいデザインスペースにアクセスし、ますます複雑な部品を生み出すことを可能にします。3Dプリンティングによって可能になる複雑さは新しい部品設計に変換するだけでなく、既存の部品設計の軽量化、およびジェネレーティブデザインツールを使用して、他の方法では作成できない完全に最適化された有機的な形状の作成も可能にします。
積層技術を使用して、自動車メーカーはわずか数日でそれらの部品の機能的なプロトタイプを作成し、数週間や数か月ではなく、設計をすばやく繰り返すことができます。また部品のプリントは、複数のパーツを1つの大きな構造に結合することで製造を簡素化し、材料の無駄を減らすという組み立ての統合への扉も開きます。
設計が完成すると、積層技術がプロトタイピングと大量生産の間の重大なギャップを埋めます。高価な工具の必要性を省くことにより、3Dプリンティングは高性能スポーツカーのような、限定生産車の為の様々なパーツのパイロットランを作成し、少数部品を生産することもでき、メーカーにとってはるかに経済的です。
部品の大量生産の準備ができると、積層技術は大量生産の為の部品の再設計をする必要がなくなり、従来の製造方法と速度及び部品あたりのコストの観点から比較できます。3Dプリンティングより、メーカーはオンデマンドで交換部品の造形やレガシーパーツを作成でき、特にヴィンテージカー用の入手困難な部品も簡単に再現できます。
3Dプリンティングのメリットは自動車製造のサプライチェーンにも拡張されます。アディティブマニュファクチャリングは、部品ではなくファイルを保持する「デジタル在庫」を有効にすることで、数兆ドルの原材料を送る必要性を減らすことができます。正確にいつ、どこで必要なのか、国境を越えてデジタルデザインを出荷しメーカーが必要な部品のみを製造できるようにします。
部品をこれまで以上により速く、より安く、より複雑にする能力。これが未来の車の製造方法です。
-
イノベーションはフォードのDNAにあります。組立ラインの移転以来、私たちはイノベーションを続け、ここで行う作業でもイノベーションを進めてきました。
(ミシガン州ディアボーンのリサーチアンドイノベーションセンター)私たちはただただ驚くべき変化の時代にいます。3Dプリンティングの技術がフォードだけでなく、他のすべての自動車メーカーへ影響を与えると思います。
未来を見据える上で、私たちは未来の工場において多くの手段を3Dプリンティングに統合することを検討しています。3Dプリンティングが製造の不可欠な部分であるような、未来の工場づくりの可能性が見えてきます。そのため、そのような規模をフォードで実現できる可能性を開いているDesktop Metal社と提携できることにとても興奮しています。
—
Ken Washington
フォードモーターカンパニー最高技術責任者
02 今日の自動車業界における3Dプリンティング
実際、自動車用途向け積層造形の初期の採用者の多くは自動車メーカーではなく、彼らが後援するレースチームでした。
何十年もの間、フォードからフェラーリまでの企業は新しい技術をテストするためのインキュベーターとしてレースを使用しています。現在新車に標準装備されている機能の多く、例えばハイブリッド車に見られる「回生ブレーキシステムやプッシュボタンイグニッション、さらにはバックミラーなどがルーツをレース場までたどることができます。
同じことが3Dプリント、特に金属3Dプリントにも当てはまります。
フォーミュラ1チーム、世界耐久チャレンジチーム、フォーミュラEチームなどは、設計の迅速な反復、 ラピットプロトタイピングの部品軽量化でレース場でのパフォーマンスの向上につながる積層造形のメリットを直接体験しました。
そして、3Dプリントはレース場で成功していますが、それにはいつも法外な費用が掛かりました。
勝利に焦点を当てているため、複雑な印刷部品の高コストを正当化することがレースチームには簡単にできますが、企業が自動車の広範囲な大量生産の部品において、費用対効果を高く3Dプリントすることはまだできません。
そうでない場合、エンジニアは3Dプリントにより、レースの為に独自の車両を作成できます。
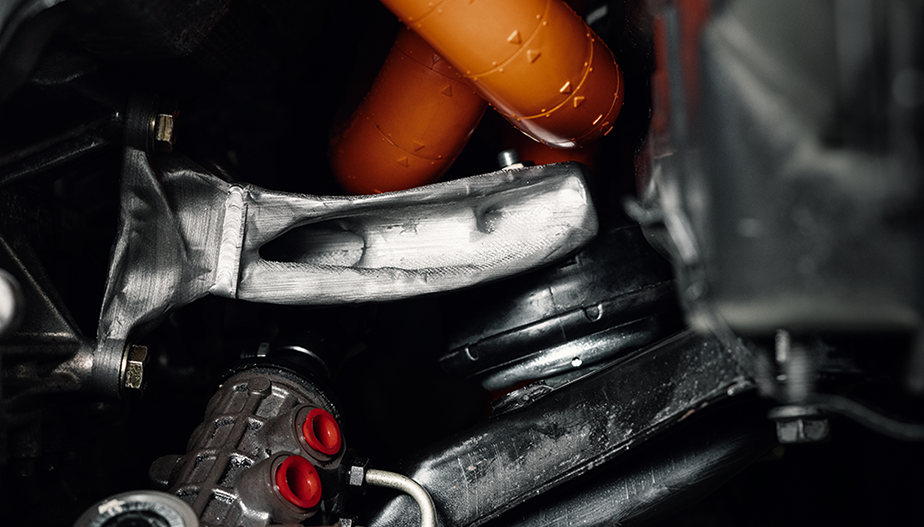
ターナーモータースポーツのエンジニアは、「これまでで最も楽しい車の運転」を実現するプロジェクトの一部として、2001年の BMW M3と最新の2013年の M3から取られたV8エンジンを組み合わせる為、独自のエンジンマウントブラケット作成に積層技術とジェネレーティブデザインを使用しました。
課題の一つは、応答性の高いステアリングは2001 M3の特徴的な機能の1つなので、ブラケットがステアリングリンケージに干渉しないようにすることでした。そのためにチームはDesktop MetalのLive Partsソフトウェアを使用してカスタムジオメトリーを設計し、ジェネレーティブデザインのカスタム部品を作成しました。
03 幅広い採用を阻むものは何か?
金属部品を3Dプリントすることの利点が非常に明確なのに、なぜ自動車メーカーはまだ採用していないのでしょうか?
基本的にそれはコスト、材料、スピードの3つに要約されます。
現在まで、多くの金属3Dプリンターはレーザーが金属粉末の薄層を溶かしレイヤーごとにパーツを形成する、レーザー粉末床融合方式に依存しています。これらのシステムには、大規模な先行投資が必要です。機器に100万ドル以上、そしてそれを使用するために必要な設備など、年間わずか1tの部品を生産するには、その費用を十分に正当化できません。
また、プリントするたびにこれらの部品には、徹底的な後処理工程が必要です。それはサポート構造を削除し、部品あたりのコストを高くします。
このシステムには、互換性のある材料の範囲も限られており、低酸素金属粉末でのみ使用できます。原材料のコストは1キログラムあたり60ドルにも達する可能性があります。部品を完成させるには1キログラムあたり数百ドルかかる可能性があり、大量生産にはコストが掛かりすぎます。
スピードに関しては、大量生産と比較すると単純に遅すぎます。最速のレーザー粉末床融合方式で、1時間あたりわずか100立方センチメートルのみ造形できます。
結果として、コスト、材料、速度の課題により自動車製造への侵入はわずかなものとなり、ほとんどの部品は、鋳造、鍛造、機械加工、プレスなどの従来の方法で製造され続けています。
04 Desktop Metal™ のソリューション
Desktop Metalが開発した3Dプリント技術はこれらの問題などを解決する準備ができおり、自動車メーカーがこれまで以上に広く積層造形を使用できるようにします。
Desktop Metal製品は、少量の機能プロトタイピングから大量生産、さらにはアフターマーケットやスペアパーツまで、自動車製造ライフサイクルのあらゆる段階に対応します。
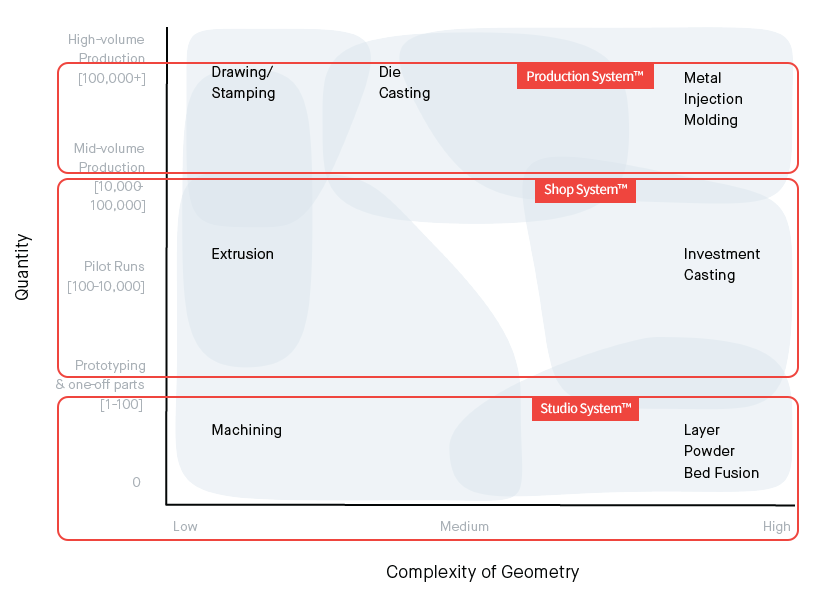
04 — The Desktop Metal™ Solution
プロトタイピングと少量生産製造:Studio システム
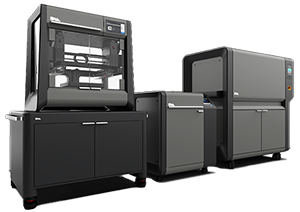
自動車メーカーの新しい車の設計と製造の初期段階においてStudio システムは優れたスタートとなります。
それは、このシステムが社内で無数にある部品のプロトタイプを迅速に作成し、多くの場合に長くて費用のかかる設計サイクルで時間とお金を節約できる理想的なツールとなるからです。
その結果、収益の増加だけでなく、企業のさまざまなアイデアをすばやくテストし、新しいジオメトリックの可能性を探索でき、企業が設計と検証から生産に迅速に移行できます。同時に、材料の無駄を減らすことでコストを削減するのにも役立ち、単一のマシンの操作に専念するスタッフの必要性を排除します。
Studio システムのメリットは、次の交換部品の市場にも広がります。
全ての車において、さまざまな部品が摩耗し、最終的には交換する必要があります。Studio システムによって既に存在しない可能性があるヴィンテージカー用の入手困難な部品などを含む、さまざまな車種やモデル向けの部品を修理工場が現地で製造できる可能性があります。
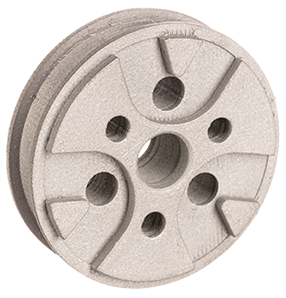
[部品例]
ショックアブソーバーピストン
-
ショックアブソーバーはショックアセンブリの動きを減らすためのダンピングを提供します。また、複雑な内部チャネルを通して油圧作動油を導くことによって、スムーズな乗り心地を提供します。
内部形状が複雑なためピストンを複数の部品から組み立てる必要があった従来の製造とは異なり、Studio システムは、パーツを1つのステップで印刷し、リードタイムの短縮とコストの削減ができます。
-
3Dプリントに伴う自由なジオメトリックにより、メーカーは素早く試作を行うことができ、コストのかかるジョブショップに作業をアウトソーシングする必要なく、新しいピストンの設計検討ができます。
Studio システムでの部品のプロトタイピングは量産への移行もスムーズにし、Shop システムやProduction システムなどの量産用のシステムが、同じように複雑なデザインであるそれらの部品を生産することができます。
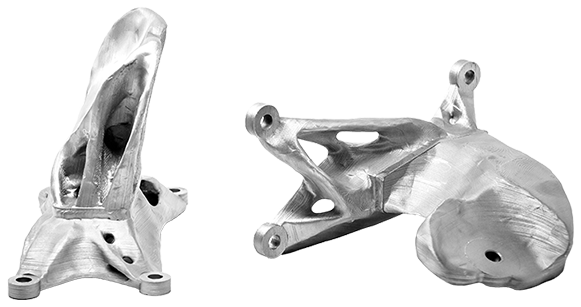
[部品例]
エンジンマウントブラケット
-
他のエンジンマウントブラケットと同様に、ここに示されている部品は車内でエンジンを保持するために使用されます。しかし、乗用車に見られる標準部品とは異なり、これは非常に特定の目的のために設計されました。
-
「これまでで最も楽しい車の運転」を実現するプロジェクトの一部として、ターナーモータースポーツ向けに設計されたこのマウントは、チームが2001年の BMW M3と最新の2013年の M3から取られたV8エンジンを組み合わせる為、特別に設計されたものです。
-
ただし、2001年のM3の特徴的な機能である応答性の高いステアリングはステアリングリンケージに干渉しないようにするため、新しいエンジンマウントにカスタムジオメトリーが必要でした。
それを作成する為に、ターナーは既存のマウントをスキャンし、Studio システムを使用して印刷する前にマウントの形状を最適化するDesktop MetalのジェネレーティブデザインソフトウェアであるLive Partsを使用しました。そしてカスタムジェネレーティブブラケットを既存のすべてのジオメトリを正常に回避し、車に取り付けることに成功しました。
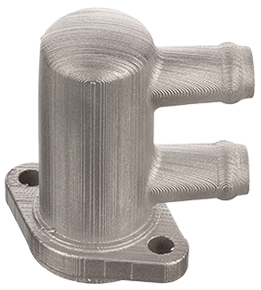
[部品例]
サーモスタットハウジング
-
車のサーモスタットの機能はエンジンが作動温度に達するまで、ラジエーターへの冷却液の流れを遮断することです。エンジンをすばやく暖めることにより、サーモスタットは、摩耗、堆積物、排出物を減らすのに役立ちます。
このサーモスタットハウジングは元々鋳造されていましたが、交換部品の需要が減少するにつれて製造中止となり、部品の入手が困難になりました。
-
パーツを再現しようとすると金型で挫折し、それを生産するために使用されたツールはもはや存在しません。そして機械加工には複雑すぎる形状でした。
ただしStudio システムを使用する場合、アフターマーケット部品サプライヤーはこのハウジングのような珍しい部品をすばやく再生産でき、それらを望んでいる自動車愛好家のために利用できるようにします。
04 — The Desktop Metal™ Solution
中規模製造:Shop システム
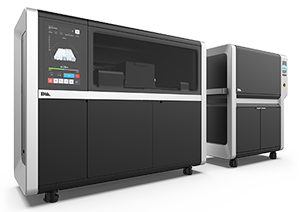
メーカーが特定の部品数十万個ではなく、数千個を必要とする場合Shop システムが少量のプロトタイピングと大量生産の間のギャップを埋めます。
理由はいくつかありますが、メーカーは大量生産を行う前に少ない数の部品を必要とする場合があります。
特定の車両の生産の初期、自動車メーカーは最終的に数十万で生産されるかもしれないものでさえ、大量生産に入る前の製品および市場テスト用にパイロットランとしてわずか数百台の車を作る場合があります。
別のケースでは、フォードのマスタングシェルビーGT500のような高性能車は多くの場合、限られた数で生産されています。2010年に、フォードではたった2,000台の車を製造したように、どの部品も数千個を作るだけでよいのです。
メーカーではすでに販売された車のラインをサポートするために、車両総数のごく一部の部品を製造する必要があり、Shop システムを使用する場合があります。
一方、アフターマーケット部品については、クラシックカー用の入手困難な部品など特定の部品の数百だけの需要がある場合があり、必要な個数はさらに少ないかもしれません。
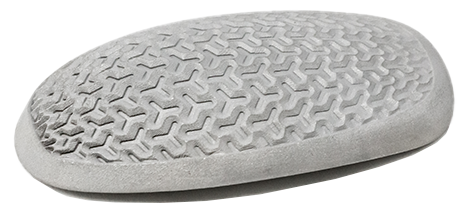
[部品例]
ギアシフター
-
ほとんどの車では、マニュアルトランスミッション車のシフトアセンブリに取り付けられている金属レバーのシフターはギアスティックで唯一の目に見える部分です。
車内のカスタマイズで長く人気のあるパーツで、カスタムアフターマーケットで、ビリヤードボールから野球ボール、そしてその間のすべてのものが作成されています。
-
ここに示されている部品は、あくまで新車購入時の1つのオプションですが、積層技術を使用すると、シフターをカスタマイズするオプションを顧客に提供できます。
多くの車のシフターはプラスチックで作られていますが、この部分は、シフターに豪華さやハイエンドな外観と感覚を与えるために金属を使用してプリントされました。
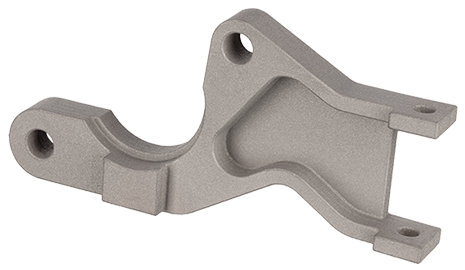
[部品例]
パーキングブレーキブラケット
-
車両のパーキングまたは緊急ブレーキアセンブリの一部で、ドライバーが解放するまで、ブレーキをかけ続けるために使用されます。
このブラケットは他の従来の方法では作成が難しい複雑な形状で、通常は金属射出成形(MIM)を使用して製造され、金型の長いリードタイムへの対処がメーカーへ強いられます。
-
Shop システムを使用すると、自動車メーカーは金型を完全に排除することができ、これらのリードタイムを劇的に短縮し、部品をより早く市場に出すことを可能にします。
Shop システムはさらに、金型の初期費用のバランスを取るために何千もの部品を製造する必要があるMIMと比較して通常は費用対効果が高いです、小規模なプリントで部品あたりのコストを低く抑えることができます。
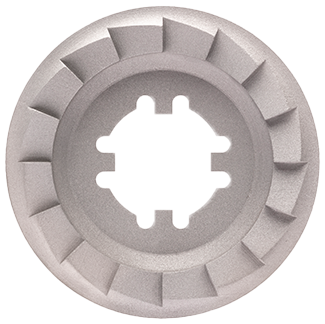
[部品例]
クラッチプレート
-
二輪車用電動スターターシステムの重要な部品で、エンジンを始動時に、クラッチプレートがスターターモーターからクランクシャフトまで回転を伝達します。
通常の装着に耐えるのに十分な強さを確保するために、これらのクラッチプレートは伝統的に鋳造または鍛造によって製造されていたため、複雑さが制限されていました。
-
しかしプレートを3Dプリントすることにより、メーカーはこの部品の斜角の歯のようにより複雑な形状の部品を設計することができます。
そして、積層造形が鋳造または鍛造に必要な金型の必要性を排除するため、メーカーはリードタイムを劇的に短縮でき、より速く部品を生産することを可能にします。
04 — The Desktop Metal™ Solution
大量製造:Production システム
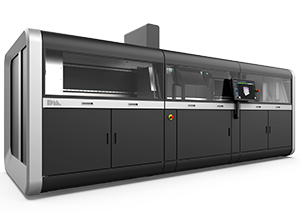
量産が必要な部品について、自動車メーカーはProduction システムを利用できます。
積層造形の重要な利点の1つは金型を排除できることです。エンジニアがすでに洗練されているデザインを送信できるようにする - 従来のプロトタイピングでなく、大量生産のためのProduction システムによって。
また、Production システムは従来の大量生産プロセスと競合できるプリントスピードを備えており、1回のプリントで数千個の部品を製造でき、それは鋳造、鍛造と機械加工のようなプロセスに匹敵する価格と生産率を可能にします。
低コストのMIMパウダーの使用と簡素化された後処理を組み合わせ、Production システムは、他の3Dプリンタープロセスの最大20分の1の部品あたりのコストを実現できます。これは積層造形を鋳造、鍛造、機械加工の実現可能な代替手段にします。
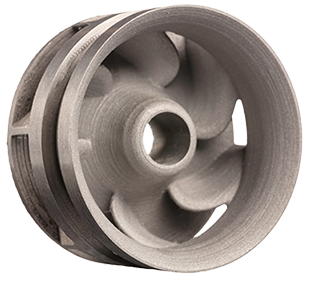
[部品例]
BMWウォーターホイール
-
このウォーターホイールは元々、自動車メーカーのDTMシリーズレースチームのために作られた、自動車用ウォーターポンプの革新的な新しいデザインでした。
標準のウォーターポンプのように、エンジンとラジエーターを介して、燃焼中に発生する熱を放散します。ただし、他のポンプとは異なりホイールは一体型として設計されており、重量を減らすことでより効率的に動作し、レース場でのパフォーマンスを向上させることができます。
-
鋳造や鍛造では作成できない複雑な形状のウォーターホイールは当初プラスチックで3Dプリントされていました。ただし、BMWはパーツをより耐久性のあるものにするために金属3Dプリントに切り替え、レーザーベースの3Dプリンターでレースカーに使用される部品を作りました。
SLMを使用してパーツを作成することは、レースチームにとってはうまくいきましたが、部品あたりのコストは、生産車には高すぎました。Production システムを使用して、BMWは一度に最大150個の部品を作成することができました。またコストを部品あたりわずか5ドルに削減し、生産車での使用がはるかに経済的になりました。
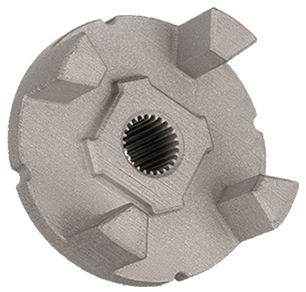
[部品例]
パワー ステアリング ジョイント
-
パワーステアリングシステムは主要な運転支援技術であり、車両のハンドルを切るのに必要な労力を減らすために油圧アクチュエータまたは電動アクチュエータのいずれかを使用します。
ここに示されているようなジョイントは電動パワーステアリングモーターからステアリングシャフトに動力を伝達するために使用されます。それは多くの場合、粉末冶金ベースの方法を使用して製造されますが、最近では脚の強度を高め、コストを削減するために鍛造することに目を向けています。
-
積層造形を使用して、エンジニアはこの部品の設計を最適化することができ、その結果15%の軽量化が実現し、脚の面取りを機械加工する必要がなくなりました。
金属3Dプリントの他の利点である、金型を排除し、リードタイムの短縮と初期費用の削減を組み合わせるとこの部品は、鍛造された代替品を置き換えるために大量生産される可能性があります。
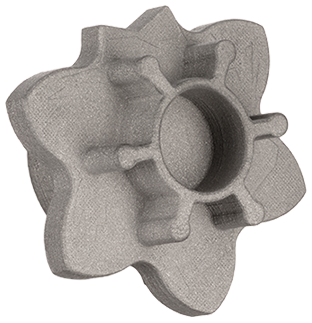
[部品例]
可変バルブタイミング スプロケット
-
バルブタイミング スプロケットは排出量を削減し効率を向上させながらトルクをかけ、エンジンの馬力を最大化するのに役立ちます。
耐久性も維持しながら、ノイズや振動、荒々しさを最小限に抑えるように特別に設計されており、それらの適切な動作を保証するため、スプロケットは厳しい公差を満たさなければなりません。
-
通常、粉末金属成形技術を使用して製造されますが、ここに示すスプロケットはProduction システムで3Dプリントされているため、従来の時間が掛かる金型工程を回避できます。