CASE STUDY活用事例
Ecrimesa Group
- コスト削減
- 開発期間短縮
- Studio システム
自動車・航空宇宙など多様な業界向けに部品生産を行うEcrimesa Groupは、膨大な数の部品生産に金型で対応していましたが、リードタイムの改善が課題でした。
00 概要
1964年に設立されたEcrimesa Groupは、最先端の技術を駆使し、スチールとアルミニウムを製造しています。Ecrimesaの技術としては、インベストメント鋳造、MIM、機械加工、積層造形を所有しています。
スペイン北部に拠点を置く同社は、現在9,000以上の製品を生産しています。顧客は世界中の自動車、防衛、航空宇宙、繊維、食品産業に及びます。
MIMプロセス開発において、世界のトップ企業である為に触媒脱バインダーを備えた連続炉、およびEcrimesa Groupの施設には最新の機械を備えており、最も効率的な技術でプロジェクトを開発できる洗練されたスタッフがいます。
01 挑戦
毎年、世界中のMIMサプライヤーは、何十億もの金属部品を製造しており、その分野は自動車産業から航空宇宙産業までの広範囲に及びます。
これらの部品を製造する各メーカーは独自の課題に直面しています。例えば、コストを削減する方法、生産の実行をスピードアップする方法、ダウンタイムを削減するために製造ラインにおいて迅速にツールを交換する方法など、悩みはつきません。
これらの課題に、Ecrimesa Groupは精通しています。
9,000を超える固有の部品のラインナップを備えた同社は、製造、保守を行う必要があります。製造工具の膨大な在庫を保有し、顧客が持ってきた新しい部品や古いデザインの変更をするための新たな鋳造型や金属射出成形金型をすばやく準備しなければなりません。
新規部品と既存部品に対する絶え間ない需要に対応するために、同社は製造ラインを迅速に改造し、且つ顧客と自社の両方のコストを可能な限り低く抑える必要があります。そのため、新しい形状ごとに新しい(金型)を必要とするためEcrimesaにとって大きな課題となります。
これらの金型は通常、その製造に8〜12週間かかりEcrimesaと顧客にとっては大きな負担となります。これらの高いコストと長いリードタイムにより、これらの部品のプロトタイプを作成することが非常に難しくなる為、顧客は金型が完成するまで最初の部品を確認できず費用と時間を浪費することになります。
それを改善するために、EcrimesaはDesktop Metal Studio Systemという次世代の製造技術に着目しました。
Ecrimesa Groupでは、我々のサービスと製品における品質及び生産性向上の弛まぬ改善に専念しています。アディティブマニュファクチャリングに対する投資はその取り組みの一つです。
Studio Systemによる設計の自由と工具を選ばない製造手法により、顧客のニーズに対応した正確に調整された部品を製造することができます。従来の製造方法にかかるリードタイムと工具費をかけることなく機能的なプロトタイプを作成することができます。
—
Eduardo Valenzuela
Commercial Engineer
Ecrimesa Group
02 Studio System による成功
EcrimesaのStudio Systemへの投資をすぐに決断しました。
Studio Systemを使用すると、同じ粉末を利用したMIM(金属射出成形、焼結プロセス)により製造されたものと比較しても特性と表面仕上げにおいて非常に類似した素材でパーツを簡単に造形できます。
射出成型するMIMとは異なり、工具を必要とせずこの材料を一層ずつノズルから押し出して成形します。EcrimesaのエンジニアはCADファイルをアップロードするだけで、数時間で焼結炉へ入れる部品を準備できます。
顧客のプロトタイプを作成することに加えて、Ecrimesaは自動車、防衛、錠前屋、産業機械向けの部品製造において、金型を使用する工程における焼結試験用のプロトタイプ部品を開発する目的においてもシステムを使用しております。
03 なぜDesktop Metalなのか?
-
Studio Systemに投資する際に、Ecrimesaは他のさまざまな3Dプリンター技術を調査しました。また、消失鋳造用の主型を作成するためにワックスプリンティングシステムにまで投資しました。
ワックスシステムの3Dプリンター技術は既存の製造方法を補完するのに役立つが後工程で鋳造が必要となるモデルに限定されました。
より一気通貫の解決策を探るため、同社は金属3Dプリンティングの更なる調査を開始しました。異なる企業やプリンティング方式で様々なベンチマークをしました。
最終的にDesktop Metal Studioに投資するという決定がされたのはStudioで造形したパーツが優れた密度であり、焼結後の歪みを最小限に抑えられた為です。
04 製造部品と比較
従来の製造方法ではMIMのプロトタイプは機械加工によって製造される為、高コストになり複雑ではない一般的な形状になります。
Studio Systemを使用するとこれらのプロトタイプをはるかに迅速に、工具に多くの投資することなく、低コストで、顧客は部品の機能をテストし、設計を繰り返すことができます。
これまで以上に広範な機能テストを可能にすることにより、金属3Dプリンティングはメーカーが従来製造されている多くの部品よりも優れた部品を開発するのに役立ちます。
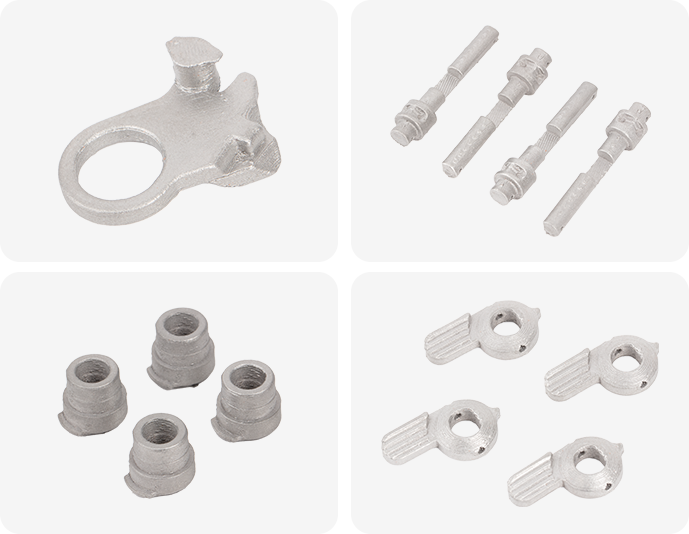
部品設計を検証する目的で作成された部品は、EcrimesaがStudio Systemの機能を検証する のにも役立ちました。
このシステムを使用して、同社は非常に幅広い部品を作成することができました。それはシリン ダーからオープンリング、刻み目のある表面まで、さまざまな形状に至ります。
スタジオシステムは工具不要のため、Ecrimesaはこれらの部品を迅速に製造するだけでなく、 リードタイムと部品あたりのコストも大幅に削減され、Ecrimesaと顧客は、設計を繰り返す機 会が増え、その結果、パフォーマンスの高い部品が出来上がります。
これらの部品は、靭性、高い疲労強度、耐摩耗性と耐衝撃性といった特性がある4140クロムモ リブデン鋼で造形されました。
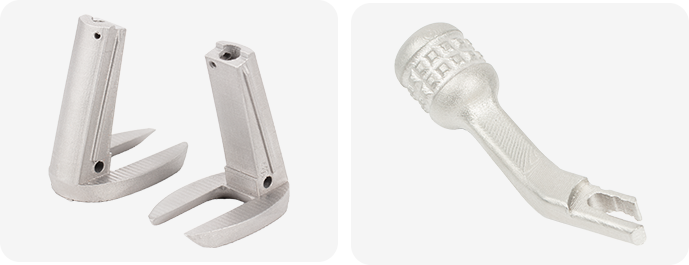
上図の部品は一般消費者向けのハンドル(左)と防衛産業向けテスト部品(右)であり、生産に取り組む前のプロトタイプ設計として、顧客が機能を探求できるように造形されています。
Studio Systemを使用して、従来の製造手法よりもEcrimesaは両方の部品を大幅に早く作成することができました。それにより、顧客がテストや設計変更する機会が増え、より優れた性能の部品となります。
これらのプロトタイプを仕上げるのに従来の方法では数週間または数ヶ月かかりまが、StudioSystemは工具が不要のため、数日で完了します。大幅に少ないコストでよりはるかに短い時間で生産できます。
これらの部品は、その高い強度と高度の特性を生かした17-4PHステンレス鋼を使用して造形されており、耐久性の高い部品になります。
05 評価
Ecrimesaにおける、Studio Systemの導入効果はすぐに現れました。わずか数日でデジタルデザインから造形された金属部品を顧客へ届けることが可能になるため、迅速で機能的なプロト タイプを使用して開発タイムラインを大幅に短縮し、そして最終的にはより良い最終設計を生み出しています。
従来の製造方法では、一つの部品が製造される前に製造用の工具準備に数週間かかるためプロトタイプを作る量は減少していました。機械加工されたプロトタイプの場合、小さな部品サイズで複雑な機能が追加されるとコストが大幅に上がります。
一方、積層造形によって提供される拡張された設計の自由により、Ecrimesaはパフォーマンスが向上し、エンドユーザーの正確なニーズに合わせてカスタマイズでき、アンダーカット、ラティ ス、ジェネレーティブデザインなどの従来の製造上の制約を受けない為、特殊な設計の新しい部品の開発が可能になりました。