Surface Activated Bonding
Bondtech developed a technology to enable the bonding in a low vacuum or the atmosphere under the instruction of Professor Tadatomo Suga of Tokyo University. This technology can be used for the mass production of the three-dimensional semiconductor. And Bondtech offers several surface activation methods that is properly selected by a bonding material.
Room temperature bonding technology with low pressure by surface activation
The advantage of SAB is to be able to directly bond a different kind of materials at room temperature. This will create new field of different materials, like a solar battery and a SAW filter.
Traditional room temperature bonding method is Ar bombardment in an ultra-high vacuum. This method is to remove the oxide film and contaminants on the bonding surface by Ar ions / atoms bombardment in an ultra-high vacuum, then to create dangling bond on bonding interface for the connection atoms.
After performing that on both side of bonding interface,atomic level bonding among dangling bonds is carried out by having the bonding interfacecontacted each other in an ultra-high vacuum. By this process, room temperaturebonding of different materials is achieved, such as chemical compoundsemiconductors and the like which are normallyhard to bond.
In order to avoid recontamination of the molecules, 10-10torr ultra-high vacuum was required, and it was an obstacle to shiftto mass production.Bondtech made possible to do large area uniform bonding with lower vacuumlevel by our unique treatment even in this ultra-highvacuum process.
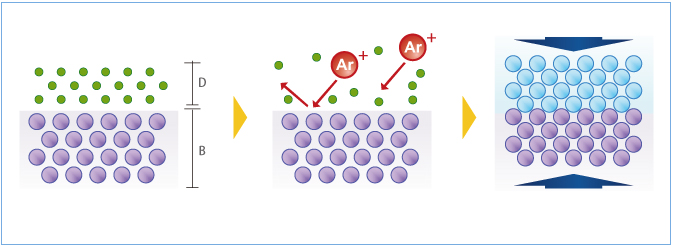
Generally SAB cannot bond the crystal ion-related materials such as the oxidation or nitride film which is materials used with a semiconductor. These materials can be bonded by Si sputtering method. In this method, crystal ion-related materials can be bonded by spattering a Si atom of the degree less than one layer thickness among the interface. In addition, this method can apply to any materials.
Improve the conventional bonding Processes by SAB
In the currently used process, by activating the surface, it can be bonded in low temperature and in a short time. Furthermore, it can obtain improvement of the alignment accuracy, the throughput and the ideal bonded interface. In this field, it is not necessarily room temperature and can expand a range of application by permitting low temperature around 150-200 degrees C.
This can be applied to conventional solder bonding. To enable diffusion in an oxidation layer, high temperature than a melting point and high pressure for breaking it are required. However it can do the ideal solder fusion at low temperature in the short time by removing oxidation layer. In addition, it can improve mass productivity because the solid-phase temporary bonding is enabled by SAB. And it can improve the productivity by dividing temporary bonding and main-bonding.
This method enables to use plasma-level surface activation with low vacuum (10-2torr) by limiting bonding material only in Au and Cu, those do not oxide or adhere easily. In addition, bonding by this method can be performed even in atmosphere in case having done within one hour.
This method is the bonding under small amount ofre-contamination like a bonding in atmosphere. Therefore the conditions inbonding is to be improved by adding a little pressure and heating at a lowtemperature<around 150 degree or less>. Asa result, the process was established enough to withstand for mass production.
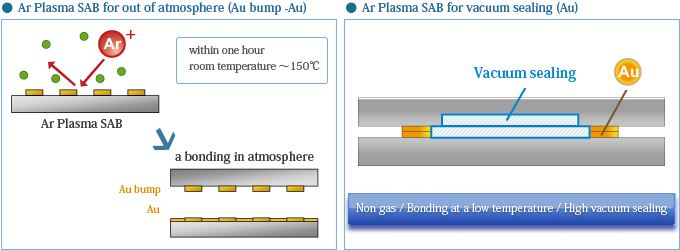
Bonding of Si, SiO2 by sequential plasma is a method to bond Si or glass in the atmosphere. This bonding method is performed with the mediation of OH radical, by attaching OH radical to an interface with plasma treatment, then making robust bonding at a low temperature annealing. Furthermore, it is possible to lower heating temperature when bonding Si at lower than 100 ℃ (in case of glass is 200℃) by having continuously implementing nitrogen radical processing after oxygen plasma processing which process has been developed by Professor Tadatomo Suga of Tokyo University.


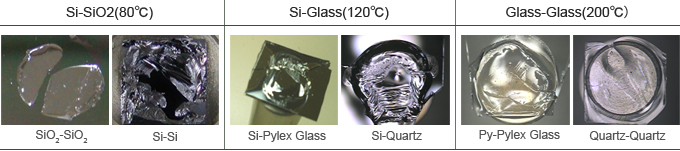
By applying hybrid bonding method using both of anodic bonding and plasma activation bonding as pre-treatment, we can achieve low temperature, void-less and low out gassing. Because the need of alkali melting which was used to necessary for anodic bonding can be decreased<OR the electric current flowing becomes 1/10~1/100 without alkali melting>, as a result of it, the out gassing of oxygen decreases drastically. Therefore no getter material to keep vacuum level is required. These are synergetic effects of the hybrid method.
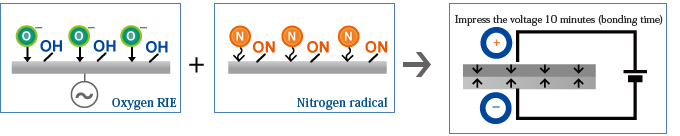
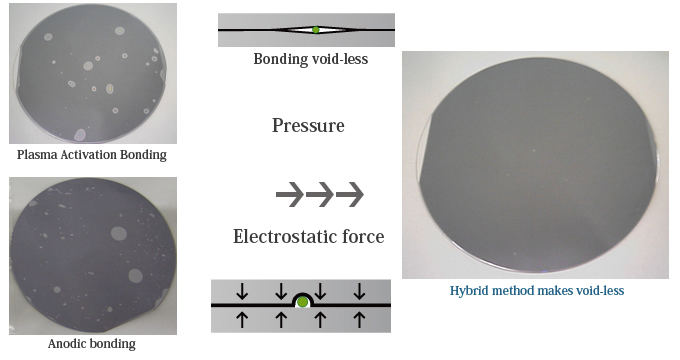
High Accuracy Alighnment technology
The wafers in a vacuum chamber are annealed at a bonding elevated temperature for out gassing, having close to each wafer, then aligned. As in conventional photolithography, position is out of place at the time of contact if positioning is performed only in the planar direction. In order to achieve accuracy after bonding, not only in the planar direction but six-axis direction positioning is required. Because of the bonding method with a distinctive alignment system comprising of a piezo-actuator, the post bonding alignment accuracy resulted within ±0.2μm. Very compact and made up of no slide member, this process can be adapted into vacuum chamber.
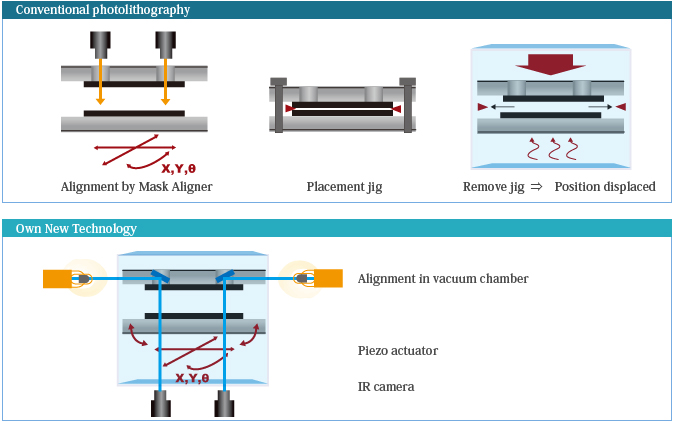