最新記事
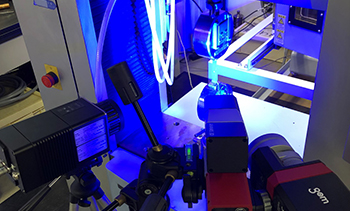
金属組織制御のためのDIC・温度分布同時測定
東京工業大学・中田研究室では、金属組織制御のためのミクロ組織の研究が行われています。その中で、GOM社ARAMISとサーモグラフィの同時測定を活用し、金属組織の挙動を可視化しています。
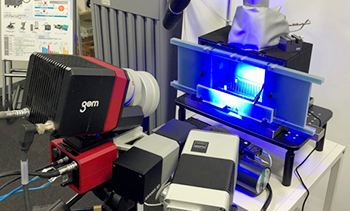
新規加熱冷却装置を用いた電子基板のDIC・温度分布同時測定
本事例では、エスペック(株)様が開発した観察窓が不要な新方式の加熱冷却装置を用い、GOM社ARAMISによる3D DICとサーモグラフィの同期測定を行うことによって、実装基板の変形と温度分布の同時評価を実現した事例をご紹介します。
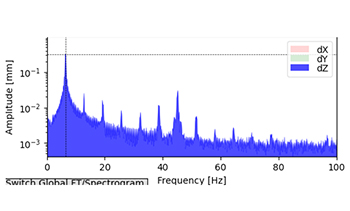
自動車のNVH対策のための非接触3D振動計測
GOM社ARAMISは非接触で対象の振動やモーションの多点同時計測が可能です。ソフトウエアは計測結果のFFT解析により、さまざまな製品の実稼働解析(ODS)によるモーダルシェイプを得ることができます。
金属組織制御のためのDIC・温度分布同時測定
最強の鉄をつくる現代の錬金術
自動車・鉄道・橋梁・高層ビルなどの我々の社会を形作る製品や構造物には、多くの鉄鋼材料が用いられています。鉄鋼材料の性質は、不純物元素の存在のほかにも、結晶粒などのミクロスケールの金属組織に依存して大きく変化します。この合金成分を調整したり熱や力を加えたりすることで、金属組織を任意に制御し、金属の特性を使用目的に適したものに自在に変化させることができます。
東京工業大学・中田伸生先生の研究室では、このいわば現代の錬金術と呼べるような金属組織の制御技術によって、より強く靭やかな鉄鋼材料をつくることを目指し日々研究を進められています。
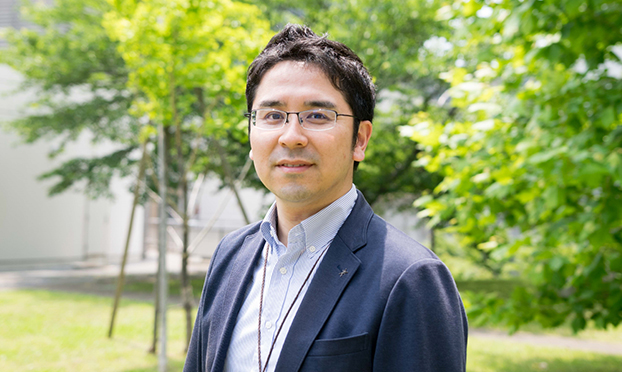
材料の複雑なミクロの特性を可視化する光学式測定技術
材料の機械的特性を調べる最も一般的な材料試験である引張試験において、鉄鋼材料、特に構造用鋼では、この応力ひずみ線図に「降伏点」と呼ばれる連続的でも直線的でもない複雑な挙動を示すステップが存在します。これはミクロの視点では、降伏した直後の少しの間は、鉄鋼材料の金属結晶格子内に含まれる炭素原子が局所的に周辺の鉄原子を押し留めるものの、ある場所で鉄原子が炭素原子を振り切ると、金属格子がスリップしてずれる(転位)ことで大きく変形し出す、というメカニズムであるとされています。この変形は局所的に発生するため、マクロ視点では試験片上に帯状に局所的に伸びる、リューダース帯と呼ばれる領域が観察されます。中田研究室では、熱処理によって金属組織の特性を変化させ、このリューダース帯の発生と伝播、および熱力学的特性がどのように変化するかのメカニズムがテーマの一つとして研究されています。
しかしながらこのリューダース帯はマクロ視点では、いつ・どこで発生するかわからない、局所的かつ過渡的な現象であったため、従来の接触式のひずみや温度の測定器であるひずみゲージや熱電対では計測することがほとんど不可能でした。
そこで中田研究室では、3D DICとサーモグラフィの2つの光学式測定技術を同時に用いることでひずみ分布と温度分布を同時に観察し、リューダース帯の発生と伝播の様子を可視化することに成功しました。
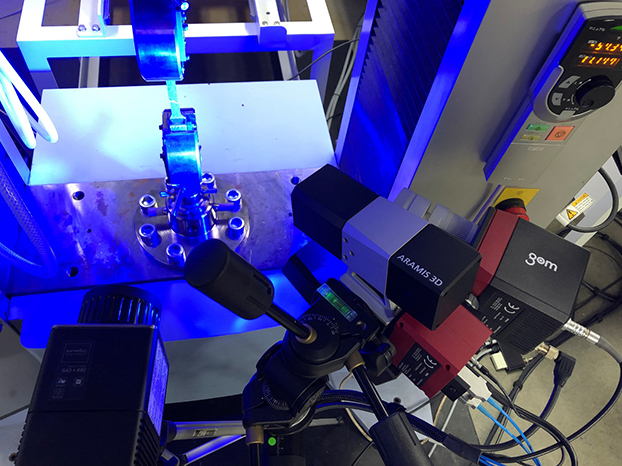
本事例では、光学式ひずみ測定システムARAMISによるDICとサーモグラフィによる温度分布の同時測定を用いてリューダース帯を可視化・定量化することで、熱処理によって金属組織の特性が意図したとおりに制御されたかを評価し、金属組織制御技術の進歩に役立てた計測事例を具体的にご紹介します。
試験と計測の条件
- 使用システム :
3D DIC測定 : ARAMIS 3D Camera 6M /MV100 (GOM社製)
温度分布測定 : VarioCAM HDx head 675 (30万画素/Infratec社製) - 試験装置 :オートグラフ(島津製作所)
- 測定対象材料 :一般的な炭素鋼を用いて、炭素を鉄の格子中に閉じ込める固溶化熱処理を実施したサンプル1、さらにリューダース変形が生じやすくする焼入れ時効処理を実施したサンプル2を準備し試験に供しました。
一般的な炭素鋼を用いて、炭素を鉄の格子中に閉じ込める固溶化熱処理を実施したサンプル1、さらにリューダース変形が生じやすくする焼入れ時効処理を実施したサンプル2を準備し試験に供しました。
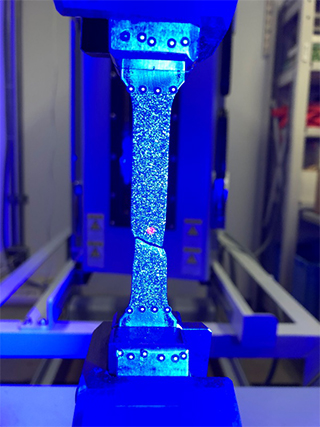
この熱処理によって炭素原子の所在が変化し、引張特性の変化がもたらされます。特に今回の条件では、降伏点における応力のピークの上昇と、そこから応力がしばらく増加せずに伸びる現象がより顕著にみられることが予想されます。そしてこの要因となるミクロ挙動の結果として、リューダース帯がより顕著に観察されることが推察されます。
計測結果と考察
引張開始から破断までを計測し、DICによる引張方向ひずみとサーモグラフィによる温度のそれぞれの分布が次の動画のように得られました。例としてサンプル1の結果を示しています。
左の分布がひずみ、左から2番目の分布が温度です。分布中の3ポイントのひずみの時間軸上の推移を一番上のグラフに、同じポイントの温度の推移を上から二番目のグラフに示しています。一番下は試験機の荷重と二点間のひずみの関係を示した荷重ひずみ線図です。
荷重と試験片形状から応力を求め、二つの応力ひずみ線図を重ねて表示すると次のようなグラフが得られました。
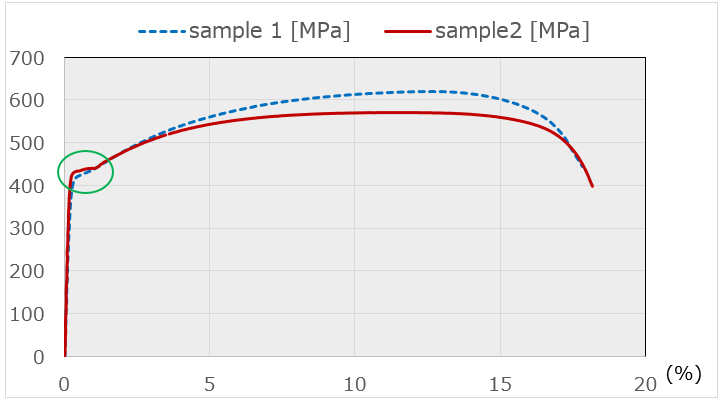
当初の予想の通り降伏点近傍において、サンプル1では降伏点から応力がどんどん増加してそのまま塑性変形に至る一方、サンプル2は降伏時の応力がサンプル1より高く、降伏点で一旦応力が増加しないまま伸びたのち塑性変形に至るという結果が得られました。
そこで次に応力ひずみ線図から得られた降伏点近傍のひずみと温度の変化の詳細を調査しました。
局所的な変化を見るために、ひずみと温度のいずれも変化速度、すなわち引張方向ひずみ速度と温度変化速度を分布であらわし、リューダース帯の発生個所の推移を可視化しました。
サンプル1については次の図のように、局所的なひずみの変化速度はそこまで早くなく、リューダース帯も少し拡散した状態で発生していることがわかります。一方で変化のあった領域を中心としてほぼ同時に温度変化が発生していることもわかりました。そして黄色の矢印で伝播の推移を示したとおり、初期にひずみ変化の発生した試験片両端に近い部位から隣接する部位へ時々刻々と伝播し、徐々に中心付近に集まってくるような挙動が示されました。同時に温度分布変化の大きい箇所もひずみ速度の伝播に伴い移動していることがわかりました。
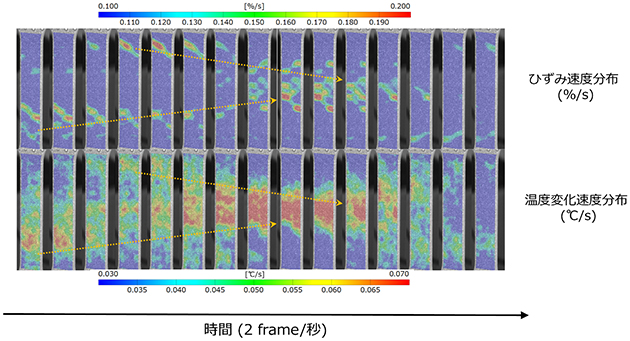
サンプル2については次の図のように、サンプル1と比べて局部的にひずみの変化速度が大きい部位が存在し、その値も大きいことがわかりました。すなわちリューダース帯はサンプル1と比べて局在していることがわかりました。またサンプル1と同様に温度変化速度の高い部位はこのひずみの変化速度の大きい部位周辺に存在し、ひずみ速度の大きい箇所の伝播に伴って移動していくことが示されました。
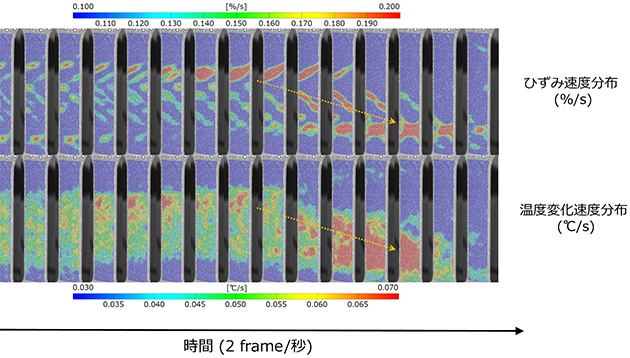
この二つの結果の違いから、熱処理によってリューダース帯の発生箇所はより局在化したことがわかりました。このことから、熱処理が鉄鋼材料のミクロ組織、特に炭素原子の所在と状態に影響を与えることで、材料の機械的特性を変化させることができたことが確認できました。
従来法に対するARAMISのメリット
微小領域の過渡的な変形を測定する場合、従来のひずみゲージでは以下のような問題がありました。
- ひずみの集中した個所をピンポイントに計測できない
- 取り漏らしを低減するために測定点数が多くすると準備工数が膨大 : 15分以上/1測定点
- 測定点数を増やすとコストが増大 : 約1000円/個
- 伸び計による長いゲージ長での測定には別途セットアップを要する : ~30分
- 大ひずみ域まで連続測定できず、大ひずみまで過渡的に変形するものは測定できない
これをARAMISによる3D DICに置き換えることで、モレのない測定による信頼性の向上とコスト低減に貢献します。
- 準備時間 : < 5分/1試験片
- 測定点数とコスト : 数万測定点/1試験片 ≒ \ 0 -
- 分布測定 : 全領域の時々刻々のひずみ分布が得られ、ひずみの集中箇所の取り漏らしがない
- 大ひずみ域まで連続測定可能
- 局所ひずみと長い標点間のひずみを同時に試験後に評価できる
引用
東京工業大学 物質理工学院-材料系 中田研究室ホームページ
https://www.espec.co.jp/products/env-test/mta/
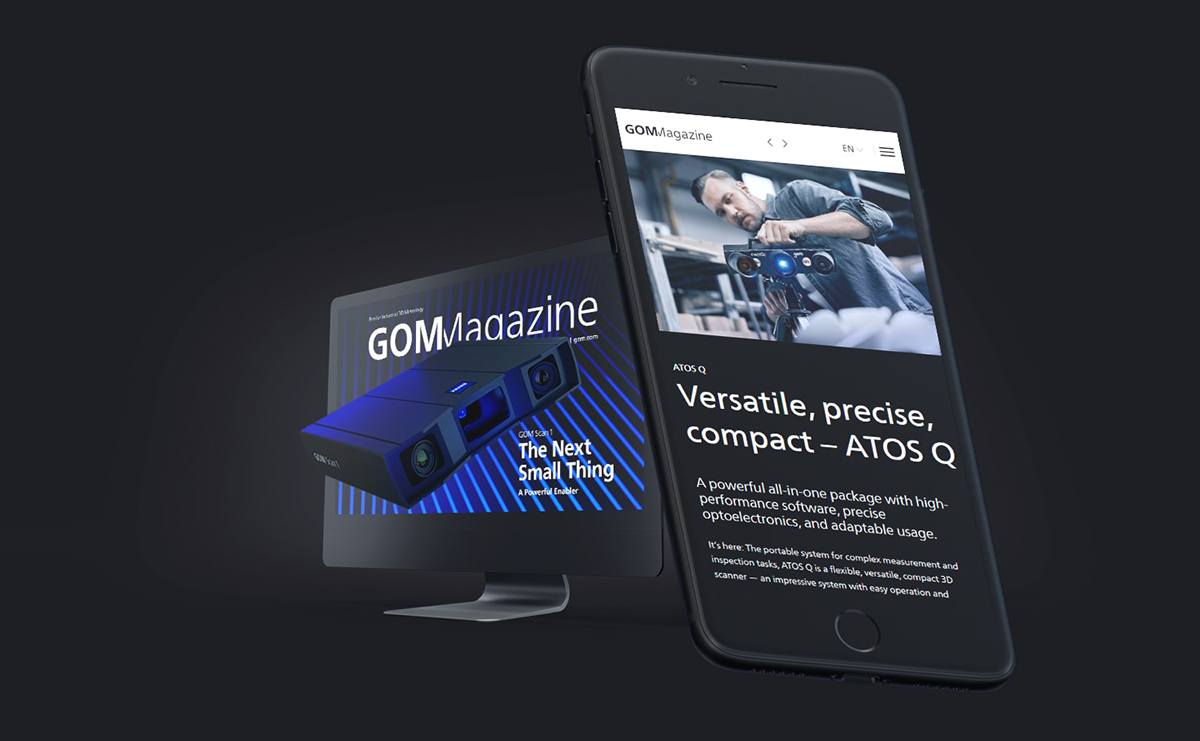
GOM社のすべてが分かる
GOM Magazine 2021
GOM Magazineは、GOM社が発行するオンラインマガジンです。GOM社の最新トピックスや導入事例といった内容を全40ページに渡って、詳細にご紹介しています。日本語版PDFを入手できるのは日本における総販売代理店を務める弊社サイトのみになります。
ダウンロードはこちら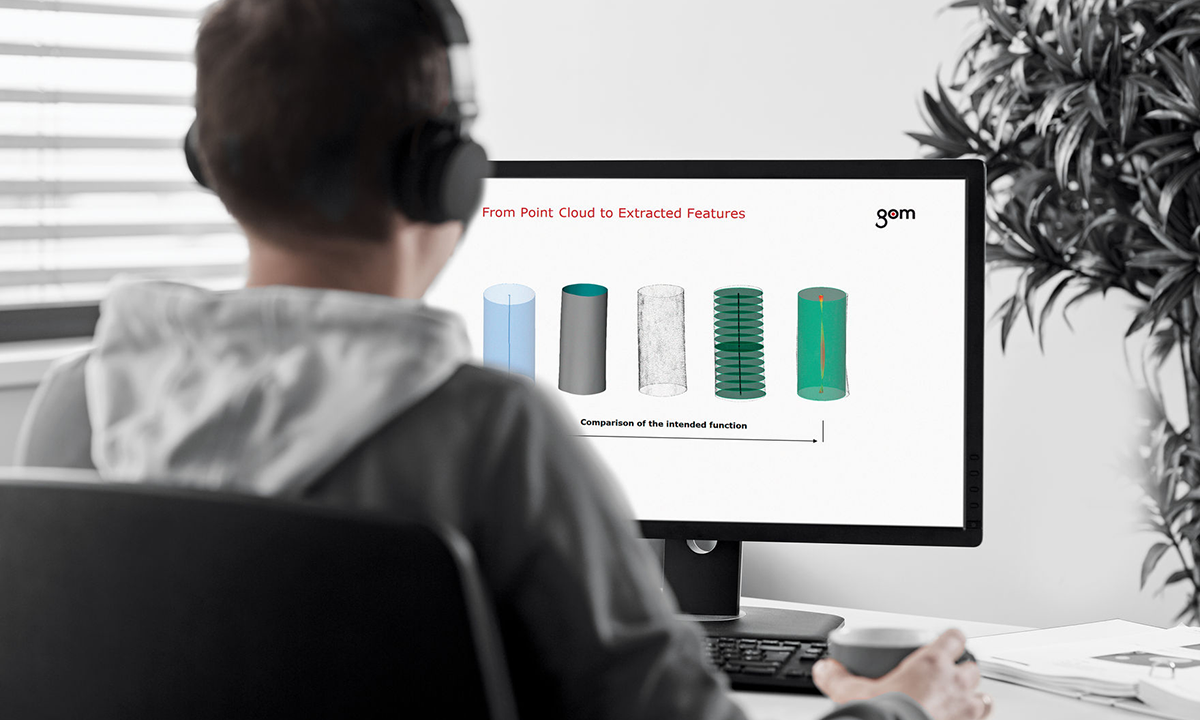
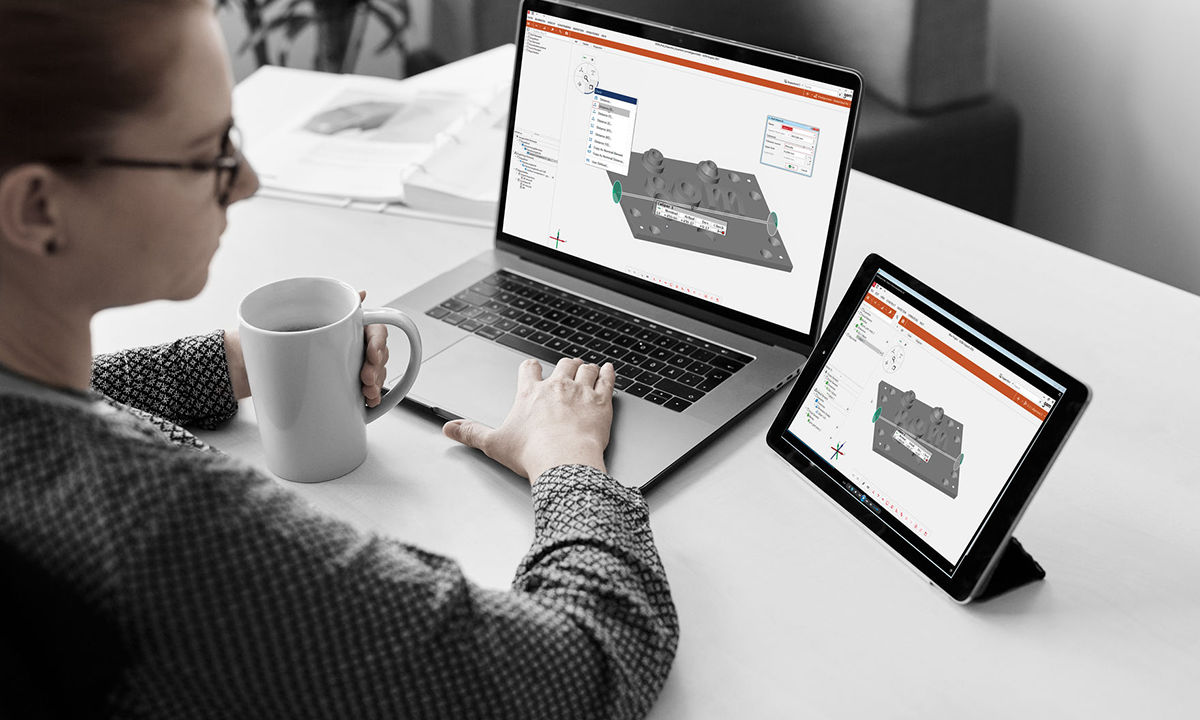
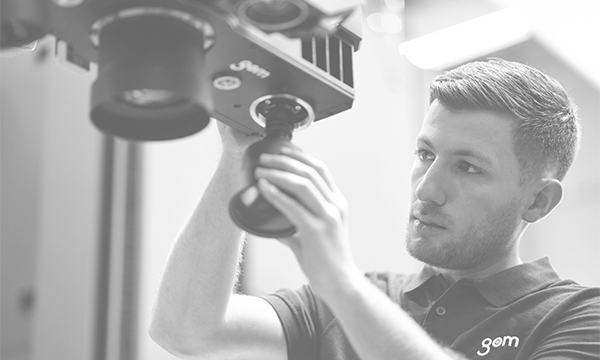
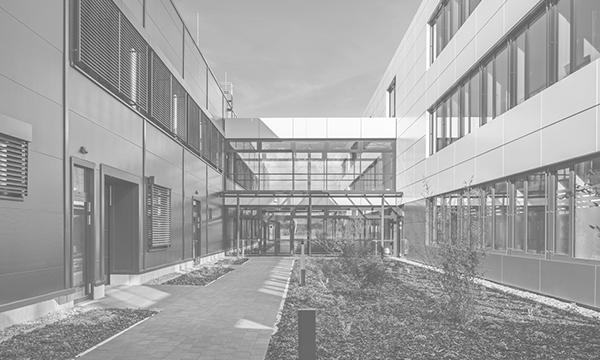